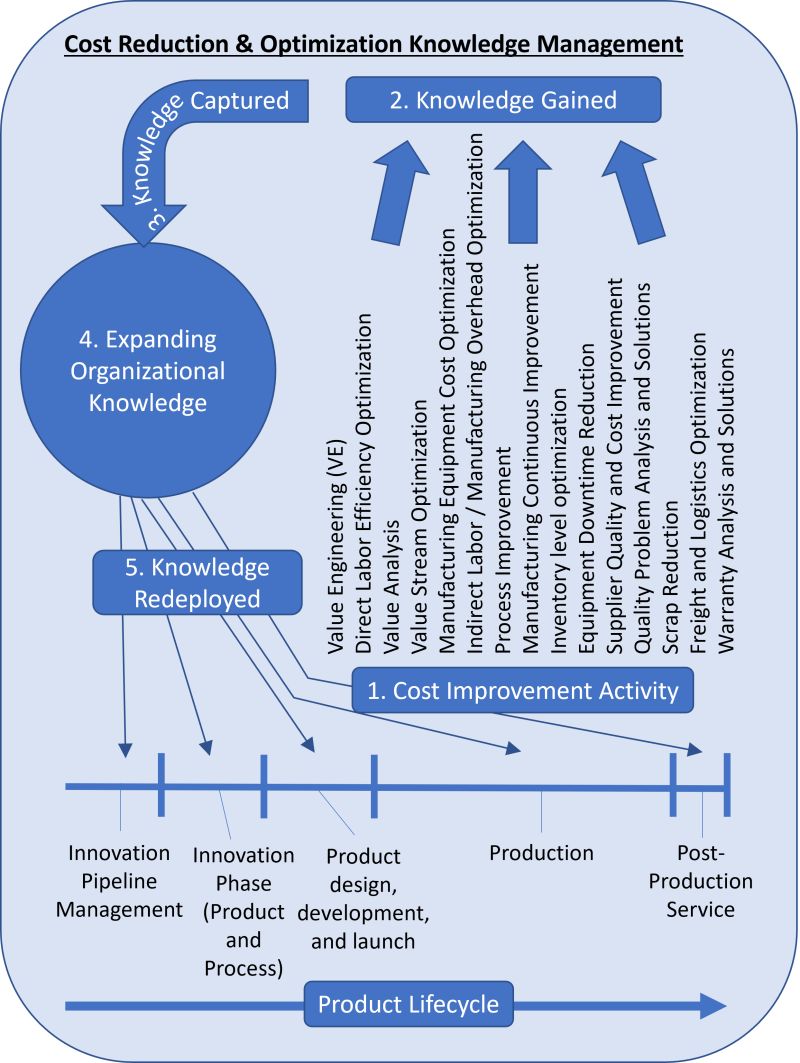
5 Steps to a Continually Improving Cost Reduction and Optimization Capability
By Craig Theisen
Most companies have cost reduction / cost optimization activity occurring at points along their product lifecycle continuum. The continuum spans from their innovation pipeline to post-production service of products in the field. For example, value engineering might be deployed on products in development, value analysis on products in production, and warranty analysis and improvement on products in the field.
There is valuable knowledge gained from each cost reduction or optimization activity. It is valuable when this knowledge gained is captured and redeployed for optimization of new products. It is a lost opportunity when the knowledge is not made known throughout the company to prevent the need to reinvent a similar cost reduction / optimization elsewhere in the company or later in time.
The illustration shows how companies can implement a process from which they continually learn and more effectively reduce product cost. There are 5 key steps in the process as labelled:
1. Cost improvement activity is performed on products somewhere along their product lifecycle
2. Knowledge is gained from the cost improvement activity
3. The knowledge gained is captured (through databases, experts, or combinations of these)
4. The captured knowledge is added to expanding organization knowledge
5. The knowledge is redeployed to innovation, new, and existing products along the product lifecycle
Companies that don’t manage their cost reduction and optimization knowledge by capturing it, sharing it, and redeploying it risk under performance in cost optimization. They may require reinventing cost improvements deployed in the past and lack ability to reach higher to more complex types of cost improvement as resources are being wasted on reinvention.
Setting up a company wide cost improvement and optimization knowledge management process is simple, and companies can customize it. To work effectively, the process should include a leader that can organize and communicate well. It is important that new knowledge is fed into the company knowledge base from which knowledge is effectively deployed along the product lifecycle.